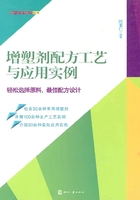
1.4 丁醇
一、概述
丁醇分子式C4H10O,化学式CH3(CH2)3OH,分子量74.12。外观为无色透明液体,有特异的芳香气味。闪点(开口)40℃,沸点117℃,熔点90℃,沸点117.25℃,相对密度,燃烧热2673.2(kJ/mol),临界温度287℃,临界压力4.90MPa。饱和蒸气压0.82kPa(25℃),折射率
,自燃点365℃,黏度2.95mPa·s(20℃)。20℃时在水中的溶解度为7.7%(质量分数),水在正丁醇中的溶解度20.1%(质量分数)。与乙醇/乙醚及其他多种有机溶剂混溶。蒸气与空气形成爆炸性混合物,爆炸极限1.45~11.25(体积比)。与水可形成共沸物,共沸点92℃(含水量37%)。
常说的生物丁醇指采用生物质原料生产的丁醇。目前主要采用发酵法获得。
二、生产技术
1.化学合成法
丁醇的工业生产有化学合成法和发酵法(生物丁醇)。化学合成法主要为丙烯羰基合成法、乙醛醇醛缩合法。工业上丁醇常与辛醇同时生产,统称丁辛醇生产。
(1)乙醛缩合法。二次世界大战期间德国开发了乙醛缩合法。优点是反应压力低,可任意调节丁辛醇生产比例,且不生成副产品异丁醇等。但工艺流程长,收率低,成本较高,故在国外也已被淘汰。
(2)羰基合成法。又称氢甲酰化合成法,是当今最主要的丁辛醇生产技术。将丙烯、一氧化碳和氢,经钴或铑催化剂羰基合成反应生成正丁醛和异丁醛,经加氢得正丁醇和异丁醇。工艺步骤如下。
①丙烯氢甲酰化得丁醛,粗醛精制得到正丁醛和异丁醛。
CH3CH‖CH2+CO+H2→CH3CH2CH2CHO+(CH3)2CHCHO
②正丁醛和异丁醛加氢得到产品正丁醇和异丁醇。
CH3CH2CH2CHO+H2→CH3CH2CH2CH2OH
③正丁醛经缩合、加氢得到产品辛醇。
(CH3)2CHCHO+H2→(CH3)2CHCH2OH
根据所采用的压力和催化剂的不同,羰基合成法分高压钴法、改性钴法、高压铑法、改性铑法等工艺,其中改性铑法具有温度低、压力低、速率高、正异构比高、副反应少、铑催化剂用量少、寿命长、催化剂可回收再用以及设备少、投资省、丁醇和辛醇可切换生产等优点。
低压羰基合成工艺(LPO)采用油溶性三苯基膦(TPP)配体改性的铑为催化剂,产物丁醛靠大量未反应的合成气和丙烯从反应釜中带出,从而实现产物和催化剂的分离,称为气相循环工艺。为减少大量气体循环而带来的能量消耗,20世纪80年代初成功开发了低压羰基合成液相循环工艺,即反应产物丁醛和催化剂溶液一起自反应釜排出,然后对产物丁醛和催化剂溶液进行气化分离。该工艺开发的吸附回收液相工艺采用的是铑/亚磷酸盐络合环氧化物催化剂,在相接近的反应温度下的反应压力更低,由于原料转化率极高,故可使烯烃氢甲酰化反应实现一次性转化,而不必循环。
由壳牌公司开发,使丙烯直接转化成丁醇、异丁醇和2-EH (异辛醇)。以三苯基膦3-间磺酸盐做配位体对铑催化剂改性,称为水溶性铑催化剂。这种催化剂具有催化剂与产物容易分离、产物正异构比例高的特点,而且用水做溶剂既便宜、安全,又有利于环境保护。可以采用在均相反应使用超声波以增加反应界面的表面积、使用极性有机溶剂和特制的配体等改进方法可以使反应均匀与高效进行。
丁辛醇生产关键是开发更好的催化剂以减少副产物、提高目标产物,达到绿色、高效的目的。因此丁辛醇的生产技术重点在于高效催化剂的开发,另外调整反应条件也是选择之一。
生产实例一:减少饱和缩醛技术
美国专利4788325描述使用相应的催化剂得到相应的饱和缩醛。美国专利4658069涉及过程转换中还含有烯丙基醚,专利提到了合适的催化剂是在所述的反应条件下,只形成少量的饱和缩醛。
本法在于提供一种经济的过程,尤其是在这个过程中形成的副产品量小,或这些副产品本身应该是可取的商业产品,此过程灵活。反应的新工艺,没有必要使用昂贵的贵金属催化剂。
可用的催化剂是质子酸或钯-膦配位体、过渡金属膦-镍配位体。
使用的质子酸可以是盐酸、硫酸、磷酸、高氯酸、氢氟酸、甲磺酸或对甲苯磺酸,但最好使用新型改性有机或无机阳离子交换的质子酸。在美国专利4440871,4310440,4567029, 4554143,4500651,4873017,4891458中首选的是无机固体β沸石或Y型沸石。
生产实例二:获取更高的正异构体技术
采用丙烯低压羰基合成铑膦络合催化剂、合成气净化催化剂和丙烯净化催化体系用于丙烯羰基合成反应。与铑-单膦催化体系相比,铑浓度由200mg/kg降到80mg/kg,配体浓度由12%降到1%~2%,正丁醛与异丁醛的摩尔比例由10∶1提高到21.5∶1。
生产实例三:氢化过程优化技术
在含有约9%~10%(质量分数)异丁醛的基础上,原油中的正丁醛经高价金属膦配体催化丙烯氢甲酰化获得纯醛。氢化过程使用的催化剂为多孔钴催化剂,其中含有至少93.0%的钴组分以及质量分数不超过6.0%铝、0.7%铁和0.8%镍。该催化剂负载量为8%~10%(质量分数),在反应器液相反应混合物的停留时间接近40min。原油加氢反应产物现场抽取样品。用于氢化改性催化剂包括35%铜(质量分数),31%铬(质量分数),2.0%钡(质量分数)和2.5%锰(质量分数)。
氢化前,将催化剂于300℃下活化到不再生成水为止。在反应温度为135~138℃及氢气压力为400psi压力下加氢并连续搅拌,搅拌速度为1750r/min。用于氢化的原料组分为430份(重量份)的正丁醛、5000份含丁醇的原油以及微量KOH溶液。氢化时,控制反应器中的氢气压力为40bar,进入催化剂床层温度为103℃,在第一反应器出口温度为132℃,反应器运作180天,获得粗丁醇。

另一种催化剂组分为24%镍(重量计,以氧化镍计算),8%的铜(以氧化铜计),2.0%的锰(以二氧化锰重量计),用66%重量的SiO2为载体。氢化前,将催化剂于300℃下活化到不再生成水为止。氢化时,将500份(重量份)的正丁醛、5000份丁醇的原油(重量份)及15份水加入氢化器内,混合物中含有微量KOH溶液。氢化时,控制反应器中的氢气压力为40bar,进入催化剂床层温度为126℃,第一反应器出口温度为150℃,反应进行142天,获得以下组分。

在德国专利DE-3228 881, DE-26 28 987和DE-24 45 303中,醛催化加氢以获得醇,使用多样性铬、锰、铁、钴、镍或铜催化剂,醇作为溶剂或增塑剂醇。
在反应过程中,为了避免发生醇醛加氢的不良反应,在德国专利DE-26 28 897中改进后的工艺是采用加氢进料时加水的方法。减少副产物的生成,也还包括提高加氢时的氢气压力,从而加快了加氢反应速率,同时可使总反应速率保持不变。
德国专利DE-16 43 856描述的催化剂组分为铜或镍,表面为碱金属氢氧化物,在此催化剂作用下,于pH为6~10下加氢。在专利WO 96/26173中描述了通过蒸馏净化的C3~C10醇的过程,是在碱金属氢氧化物的存在下进行蒸馏。
液相加氢进料,采用的是乙醚等稀释剂,最好使用乙醇,颗粒催化剂床的温度变化不应超过40℃,加氢反应器最好在等温条件下操作。
加氢催化剂最好选用复合加氢催化剂体系,特别是选用铼、铂、钯、铑作为催化剂的活性成分。附载材料可以是三氧化二铝、二氧化钛、二氧化硅、二氧化锆、硫酸钡。
采用改性阿德金斯催化剂组分为35%铜(质量分数)、31%铬(质量分数),进料组分为原油丁醇与正丁醛。催化剂在使用前,通氢气流在300℃下活化。氢化时反应器的氢气压力为5000Pa,进入催化剂床层的温度为103℃,第一反应器出口温度为132℃,获得的丁醇含量98.85%。
2.发酵法
发酵法产品即生物丁醇。工业化生产规模上仅次于乙醇发酵。
丁醇生物发酵是利用丙酮丁醇梭菌、拜氏梭菌、乳酸杆菌等在严格厌氧条件下进行发酵生产丙酮丁醇后进而分离的过程。
发酵法以粮食、谷类、玉米、薯干、糖蜜等为原料,加水制成发酵胶液,经高压蒸汽加压灭菌处理后,接入丙酮/丁醇菌,于35~38℃下发酵。发酵时生成气体含二氧化碳和氢气,由发酵液所得产品中,含正丁醇60%、丙酮30%、乙醇10%,再经精馏分出丁醇、丙酮和乙醇,或做总溶剂直接使用。
由发酵工段来的发酵液较稀,仅含有1.8%(质量分数)的溶剂(丁醇、丙酮和乙醇),其余部分为水和发酵固体物。由于发酵液比较脏,必须经过醪塔进行处理。醪塔塔顶产出体积比为50%的溶剂,进入乙-丙塔脱除乙醇和丙酮,乙-丙塔底部的丁醇-水混合液进入第一丁醇塔,塔顶产出的丁醇-水恒沸物[58%(质量分数)丁醇、42%(质量分数)水];进入分层器自然分层,分层后丁醇富集相[77%(质量分数)丁醇、23%水(质量分数)]进入第二丁醇塔。第二丁醇塔顶部的恒沸物经分层器分层,底部得丁醇产品。
分层后的水富集相[7%丁醇(质量分数)、93%水(质量分数)]进入第一丁醇塔富集丁醇。第二丁醇塔的进料含77%(质量分数)丁醇,塔顶产出含58%(质量分数)丁醇的恒沸物,所以第二丁醇塔塔底产品丁醇的量不太多,而第一丁醇塔塔顶部进入较低温度的水富集相,却从塔底排出较高温度的水,带走的热量很多。每循环一次,产品丁醇的量不大,带走的热量却很多,故能耗很大。要节能,应将大量的水在塔外脱去,故可以采用氟化钾脱水来富集有机产品。
发酵法生产醇,通常是先对底物进行发酵,把发酵液移出后再用有机溶剂进行萃取,所得萃取余液再循环利用。溶液萃取法难于将产物进行彻底和有效分离,且生成产率不高。
发酵法丁醇产量、产率低。①由于丁醇对菌体的毒害作用,丁醇的质量浓度<13g/L,丁醇产量<4.46g/(L·h),丁醇产率小于25%(质量分数)。②溶剂终浓度低。传统的ABE发酵,总溶剂质量分数≤2%,水分质量分数可达98%以上,采用常规精馏方法加大了设备、电力和能源的消耗,这也是丁醇高成本的关键所在。③丁醇在总溶剂中的体积比例低,一般只占60%,其余30%为丙酮,10%为乙醇,加大了后期丁醇回收、分离的成本。④传统的丁醇发酵普遍采用玉米、糖蜜为原料生产,随着粮食价格的上涨及世界粮食资源的匮乏,丁醇的生产需改用更为廉价的原料。
发酵法关键技术是原料成本、菌种选择及分离路线。针对传统丁醇发酵产业存在的问题,可从以下几方面着手,具体策略如下。
(1)改良菌株。利用基因工程和代谢工程技术,解除代谢过程中可能存在的产物或者中间产物的抑制,提高菌种对丁醇的耐受性,强化丁醇生产中的关键酶,切断丙酮、乙醇的生成代谢途径,提高丁醇在溶剂中的比例。
(2)分离技术。研究从稀发酵料液中经济、有效回收丁醇的方法,如渗透蒸发、汽提、液-液萃取等技术。
(3)高效发酵工艺商品化。用酶学、微生物生理、发酵技术等知识优化和再商品化丁醇发酵工艺。
我国应广泛利用价廉、丰富的木质纤维素资源,改良丁醇发酵菌种,采取有效的回收技术,革新生物反应器,运用生物发酵工程技术,切实提高丁醇产量和产率,降低生物燃料丁醇的成本。
生产实例四:原料选取与加工技术
丁醇的生产原料大部分采用价格低廉的可再生资源,如农业废弃物、能源作物、垃圾等。但丙酮丁醇梭菌不能直接高效地利用这些富含高纤维素物质,需经过预处理,先将它们水解成单糖,然后再发酵利用。
农业废弃物包括玉米秸秆、小麦秸秆和木屑等,它们主要是由五碳糖和六碳糖组成的多糖。在利用这些底物之前,需经过碱液和纤维素酶的组合处理。为了更好地利用酶水解液,需对丁醇发酵条件优化,选取的因素包括营养条件和环境参数,它们对丁醇发酵产生重要影响。统计分析方法在优化丁醇发酵的条件方面是高效和实用的,它通过因素间交互作用,迅速找出关键影响因素,因而被广泛应用。
2010年我国农村的秸秆产量达7.26亿吨,农业加工业的废弃物则高达8200多万吨,应研究有效的预处理方法。用来发酵产生丁醇的原料有玉米、糖蜜、乳清、葡萄糖等。近年来,一些农业废弃物,如稻草、玉米纤维等可增加微生物或酶水解木质纤维素的有效性。采用多级连续发酵、固定化发酵、细胞循环高密度发酵等方法,通过微生物对高底物浓度、发酵抑制剂、有机酸和醇的耐用性,保证微生物的活力。为提高工艺的经济性,生物反应器中的各项步骤可耦合,可通过酶/微生物糖化发酵下游技术同时生产生物燃料丁醇。
生产实例五:菌种与培养基技术
美国农业部农业研究所(USDA-ARS),已在利用拜氏梭菌转化纤维素生物质生产生物丁醇。
美国绿色生物有限公司(GBL)和专业级公司EKB公司合作,投资85.5万欧元创新丁醇发酵工艺技术,计划开发生产生物燃料丁醇用于交通运输,将其生产成本降低1/3。
加利福尼亚技术研究院下属公司Gevo、Khosla风险投资公司及Virgin Fuels公司目前已将研究从乙醇转向了丁醇;正在利用甘蔗、玉米副产物和草等不同类型的生物质生产生物丁醇。
美国Ener Genetics International Inc.(EGI)用DNA遗传改良菌株,通过代谢工程调控和专利技术开发的连续固定化反应器,采用膜技术发酵仅需6h,菌种能耐受4%~5%的丁醇,发酵液中丁醇占总溶剂的90%(传统发酵法丁醇一般占60%),丁醇产量达4.5~5.0g/(L·h),产率为40%~50%,比传统丁醇工艺产量提高400%~500%,生产成本不到0.264美元/升,车间成本500万~1000万美元,而传统丙酮丁醇发酵法生产成本为2.5美元,传统发酵车间至少需要投资1亿美元。
美国ButylFuel公司采用BFL公司专利生产的1L玉米可产丁醇0.27L,且无乙醇或丙酮产生,而目前报道的研究中1L玉米最多能产丁醇0.14~0.20L,且仍沿用ABE发酵过程。用石油生产丁醇的成本为1.350美元/升,而用玉米生产丁醇的价格为0.317美元/升(不包括所产氢气),可以和玉米产乙醇的0.338美元/升的价格相竞争。当用饲料等废弃物代替玉米时,丁醇成本可降至0.225美元/升。
可以改换不同原料的培养基,如瑞典采用榉树刨木花吸附非生长细胞,发酵培养基是葡萄糖和微量元素液,采用ATCC 824菌种。营养培养基、增殖培养基为发酵培养基中成分或做部分改变,生成总溶剂转化率为30%。
以玉米秸秆废弃物的酶水解液为底物,利用丙酮丁醇梭菌CICC 8008发酵生产丁醇,优化发酵条件丁醇发酵产量达到6.20g/L。操作实例如下。
(1)菌种与接种。将丙酮丁醇梭菌菌种在100℃下活化,热处理1.5min后接种。
基础培养基的成分(g/L):葡萄糖10,胰蛋白胨5,酵母粉5,大豆蛋白胨5, K2HPO40.5, MgSO4·7H2O 0.2, FeSO4·7H2O 0.01, L-半胱氨酸0.5。培养基在115℃下灭菌15min,热处理的孢子悬浊液在37℃条件下培养14~16h后作为接种液。
(2)玉米秸秆的预处理与酶水解。玉米秸秆粉碎粒径约为1mm,玉米秸秆纤维素含量30%,半纤维素27%,木质素低于20%。玉米秸秆的预处理:100g的玉米秸秆粉混合悬浮在1L的NaOH稀溶液中(NaOH稀溶液的浓度为3%),室温浸泡24h,固-液比1∶10,浸泡结束后,混合液用10mol/L盐酸调节pH值至7,过滤并用烘箱烘干后备用。
(3)秸秆的酶水解。1kg经NaOH预处理后的秸秆加入10L的粗酶水解液中(纤维素酶供应商:奥博星生物技术公司),酶活为4.5 FPU/g(秸秆),用浓度为1mol/L的HCl调节pH值至5。
酶水解条件:温度50℃,摇床转速100r/min,水解72h后,混合液经8层纱布过滤,在转数为8000r/min的离心机上离心分离10min,取上清液装入配有螺旋盖的培养瓶中并在-20℃下保有备用,水解液还原糖含量为42~44g/L。
(4)分批培养。丁醇的厌氧发酵是取100mL血清瓶,装液量为50mL,将50mL的酶水解液和2.5mL菌液共计52.5mL的培养物加入血清瓶中,通入高纯氮气获取厌氧培养环境,氮气预先经过装有铜丝的热石英柱的亨盖特装置。培养条件:pH值为7,温度37℃。
另外,南非选用SPO进行固定化细胞发酵生产丙酮、丁醇,反应在流动床内进行,容积含量与野生菌株游离细胞的结果相仿,容积产率为传统发酵法的10倍。发酵容积含量提高10倍。
日本选用ATCC 824菌株,培养基主成分为葡萄糖、CaCl2等。在反应器内装有海藻酸钙凝胶珠细胞,发酵温度37℃, pH值为4.5,用NaOH溶液调节。新鲜培养基用N2气保护通入反应器内,糖转化率23%。
生产实例六:分离新工艺
发酵流程中可加一分层器。分层后有机物富集相进入丁醇塔,丁醇顶部物进入乙-丙塔,将低沸点乙醇和丙酮与正丁醇分开,乙-丙塔底部物料进入分层器分层,乙-丙塔物料进丙酮塔,将丙酮与乙醇分开。分层器中水富集相进入蒸发器,将稀水浓缩成浓盐水后循环使用。
目前可以采用膜萃取工艺。在此工艺中,大量的均匀分散的疏水中空纤维微孔膜穿过发酵反应器,纤维腔内的有机溶剂能连续地萃取发酵液中的乙醇等。例如用UM-BIO(聚酰胺膜)可将生成产物提纯。
现已使用的超临界CO2萃取技术有利于快速萃取和分离乙醇。例如将CO2加压加热到7.3MPa和31℃,从发酵液中萃取乙醇,能耗仅为化学法的1/3~1/2。
与化学合成法相比,发酵法上的优势在于:①化学合成法以石油为原料,投资大,技术设备要求高;而微生物发酵法一般以淀粉、纸浆废液、糖蜜和野生植物等为原料,利用丙酮丁醇菌所分泌的酶来将淀粉分解成糖类,再经过复杂的生物化学变化,生成丙酮、丁醇和乙醇等产物,其工艺设备与酒精生产相似,原料价廉,来源广泛,设备投资较小;②发酵法生产条件温和,一般常温操作,不需贵重金属催化剂;③产品选择性好、安全性高、副产物少,易于分离纯化;④降低了对有限石油资源的消耗和依赖;⑤发酵法更体现环保和清洁生产理念,符合化工发展方向。
三、应用技术
增塑剂在塑料及薄膜中的应用
应用实例一:酯类合成技术
丁醇需求的主要增长动力为丙烯酸丁酯/甲基丙烯酸丁酯、醋酸丁酯、邻苯二甲酸二丁酯及其他增塑剂和涂料溶剂。例如用于生产醋酸丁酯的酯化法工艺如下:在装有温度计、回流冷凝管和分水器的三口烧瓶中加入冰醋酸、一定量的正丁醇和对甲苯磺酸,加热回流分水至几乎无水分出为止。停止加热,放出水层,反应结束后将反应液依次用饱和氯化钠溶液、5%碳酸氢钠溶液、蒸馏水洗涤,用无水硫酸镁干燥,蒸馏,将所得120~126℃馏分再蒸一次,按相应的沸点收集醋酸正丁酯。
用对甲苯磺酸1.0g,改变正丁醇用量进行反应。随正丁醇用量的增加,酯化率逐渐提高,当醋酸∶正丁醇为1∶3时,酯化率达到最大值。对甲苯磺酸是催化合成醋酸正丁酯的良好催化剂。它不腐蚀设备,不污染环境,反应条件温和,操作方便,是一种很有前途的酯化催化剂。
对甲苯磺酸是一种强有机酸,无氧化性,无碳化作用,作为酯化反应的催化剂,具有活性高、选择性好、操作方便、不腐蚀设备、污染少等显著优点。采用对甲苯磺酸做催化剂合成醋酸正丁酯,在适当的合成条件下产率高达99.14%。
应用实例二:生产柠檬酸三(乙氧基羰基甲)酯技术
向一个带搅拌器、温度计、回流管水分离器的1L的四口玻璃瓶内加入192g无水柠檬酸、148.0g丁醇,将该混合物在大气压力下加热至118℃,并在此温度下加热超过30min。在上述温度下保持6h后开始回流,温度上升到145℃回收生成的酯。观察在没有更多的水生成时,视为反应完成。将反应产物冷却到60℃,在此温度下加入两倍于反应产物的碳酸钠和100.0g的水,并与水分离器相接,加入147.0g氯乙酸、1.0g三乙胺和100.0g甲苯,用30min时间将反应混合物加热至120℃,直到压力达到约47kPa,回收124.0g水。反应完成后,将反应产物冷却至40℃,加入340g的1%盐酸水溶液,而氯化钠作为副产品形成三乙胺季铵盐。随后,向有机层加入两倍于反应产物的碳酸钠,将有机层与340.0g水加热到120℃,清洗回收甲苯,直到压力达到约4kPa,用蒸汽在120℃进行蒸馏,时间为1h。以同样的压力从反应产物中脱除低沸点成分,获得270.0g的红黄色透明液体。收率69.1%。产品的酸值为0.025mgKOH/g,为柠檬酸三(乙氧基羰基甲)酯,是一种增塑剂的最新产品。
应用实例三:生产乙酰柠檬酸三丁酯(ATBC)技术
将TBC(柠檬酸三丁酯)在有机酸催化下与乙酸反应,控制TBC与乙酸酐的投料比为1∶1.9,催化剂用量为0.08%,反应温度为85℃,反应2h即得ATBC粗品,粗品经精馏、碱洗、水洗、干燥,即得产品。
采用甲苯作为带水剂时,酯化时间由可无带水剂体系下的6.5h缩短为3.2h,效果显著。结合微波辐射技术催化合成ATBC。时间小于30min,酯化率达91.2%,时间较常规法缩短6倍,方法简单,节省能源,具有工业化应用前景。
对甲苯磺酸是一种强有机酸,催化活性高、用量少,不易引起副反应,产品色泽好,对设备腐蚀性和环境的污染都比硫酸小,是一种研究较多的催化剂。以对甲苯磺酸、吡啶为催化剂,采用两步法合成ATBC,在优化条件下ATBC产率94.2%。
采用共酰化-酯化法合成ATBC,乙酰化过程副产乙酸丁酯,原料利用率高,将目的产物用活性炭纤维脱色,产率98%以上,效果较好。采用对甲苯磺酸、乙酸和钛酸四乙酯的混合物(7∶2∶1)(质量比)为催化剂合成ATBC, ATBC产率达95%,产品纯度超过98%。以氨基磺酸为催化剂合成ATBC,适宜条件下,酯化率98.2%,乙酰化率91.3%。氨基磺酸性质稳定、安全易得、使用方便,可循环重复使用,有一定的应用价值。
在螺带式掺混机内将聚乳酸与乙酰TBC、防黏剂、滑爽剂相混,用双螺杆挤出机(料筒温度)170~210℃造粒。粒料在50℃烘箱内加热,然后在料筒温度为160~200℃的挤出机内熔融,以挤出机顶部T-模头挤出0.13mm厚的薄膜。将该双向拉伸膜在拉伸温度50℃,拉伸速度7mm/s,拉伸比2.5条件下,用双轴向拉伸机进行双轴向拉伸,然后在50℃热固化5min,得热收缩拉伸膜。
在预聚物反应器中,所得到的聚合物分子量约为400~2500。各种催化剂都可用于聚合,如金属氧化物、金属有机络合物、金属卤化物等。
用该工艺所合成的聚乳酸分子量为50000~200000,根据需要可调整工艺条件来控制产品的分子量。产品收率为70%~90%,大大降低了产品成本。
用含生物降解TBC组分生产的PVC制品:将100份PVC与35~60份TBC混合,使之相容,继续加入1~5份稳定剂(硬脂酸钙/锌)及其他颜料、阻燃剂[Al(OH)3或Mg(OH)2]、发泡剂(偶氮二甲酰胺)以及碳酸钙/镁等制成PVC增塑糊。