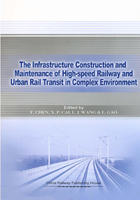
A RAPID METHOD FOR ESTIMATING THE PREVENTED TRAIN DELAYS AS AN EFFECT OF RAIL INFRASTRUCTURE INSPECTIONS
Christer STENSTRÖM1,Tao XIN2,3,4,Aditya PARIDA1
1Division of Operation and Maintenance Engineering,Luleå University of Technology,Sweden
2School of Civil Engineering,Beijing Jiaotong University,Beijing 100044,China
3Beijing Key Laboratory of Track Engineering,Beijing 100044,China
4Beijing Engineering Research Center of Rail Traffic Line Safety and Disaster Prevention,Beijing 100044,China
Abstract:In this study,a formula is described for calculating the relationship between preventive maintenance inspections and train delays for rail infrastructure.The reduction in train delays due to preventive maintenance has been calculated as follows:When an inspection is performed,the probability to find a potential failure is between 0 and 100%.The potential failure is registered as an inspection remark.The risk that the potential failure will degrade to a functional failure within a certain time is also between 0 and 100%.Strictly speaking,this time is equal to the specified maximum time to restoration in the inspection remark registration,e.g.within one week,but in practice longer.As an example,one can assume 100 inspections,with 10% probability to find a potential failure,75% risk for functional failure if an action is not taken within a near future and 25%risk for train delays.This gives 100×0.1×0.7×0.25=1.875 prevented train-delaying functional failures,and therefore 1.875 times the average number of train delay minutes in reduced minutes of train delays.A case study was carried out to verify the proposed method.The prevented train-delay minutes per maintenance inspection for various rail infrastructure systems were found to be between 0-40 minutes per inspection.However,the result depends to a large extent on the definition of inspection within the maintenance database.The result also depends on the type of inspection,e.g.safety or maintenance inspections.Moreover,the result depends greatly on the criteria that are being used for specifying the risk that a potential failure will degrade to a functional failure within a certain time period.These factors need to be clear before actions are taken upon the results.
Keywords:train delay,inspection,railway infrastructure,maintenance,failure
Email:xint@bjtu.edu.cn
1 Introduction
Proper maintenance of railways is essential in order for rail transportation to respond to passengers and freight operators’ requirements and expectations on reliable and punctual transportation[1-3].Shortcomings in preventive maintenance of railways can lead to costly corrective maintenance due to disturbances in train traffic,which in turn affects train delays and capacity.Therefore,infrastructure managers(IMs)seek continuously methods for improving their knowledge of the effects of preventive maintenance,with the aim to reach the best possible cost efficiency[4].The purpose of the present study is therefore to develop and describe a rapid method for connecting railway maintenance inspections to savings in train delays.
The study pertains primarily to describe a formula for maintenance inspections and prevented train delays,and not to carry out data analysis for assessments of results,but a case study is given to verify the requirements on the formula’s ability to calculate the effect of maintenance inspections.Therefore,the study comprises preventive and corrective maintenance data of rail infrastructure.The collected data is limited to one IM,Trafikverket(Swedish Transport Administration),and is further limited one year’s data of 65 track sections,i.e.about one third of the railway network in Sweden.The study of the data quality within the case study pertains to which degree the data fields are used,and in certain cases how the probability distributions of the data appear.
This study pertains to prevented train delay(minutes)as a function of preventive maintenance inspections,which is simpler and more cost efficient than estimating costs.Nevertheless,for monetary costs and cost savings,see Nissen[2]and Stenströmet al.[5,6]
2 Methodologies
Condition based maintenance is performed with the aim to identify and rectify potential failures,also known as inspection remarks,to prevent functional failures to occur.After rectification of a potential failure,the rectified item is expected to recover to a state similar to the state before the potential failure,i.e.as good as old,or to recover to a state similar to the commissioning state,i.e.as good as new.The failure frequencies for new or repaired items can be assessed based on the manufacturer’s data,historical working order data or expert-group estimations.Consequently,inspections and rectification of potential failures decreases the number of functional failures,and thus,prevent train delays to take place;see illustration in Figure 1.

Figure 1 Illustration of the effect of maintenance inspections.An item can be a system,subsystem or component
When an inspection is being performed,the probability of finding a potential failure is between 0 and 100%.The risk of a potential failure to develop to functional failure within a certain time is also between 0 and 100%.Strictly speaking,this time equals the time specified for rectification of the potential failure,e.g.two weeks,but in practice it is longer(further discussion in Section 3 and Figure 3).For example:assume 100 inspections,where each inspection has on average an 10%probability of identifying a potential failure;potential to functional failure probability is 75%,e.g.within one year;and the risk for train delaying functional failures is 25%.This gives 100×0.1×0.75×0.25=1.875 prevented train delaying functional failures,and therefore 1.875times the average train delay in prevented train delay minutes.The prevented train delay(benefit)in minutes will then be:

where:
α=The probability of identifying a potential failure(inspection remark),α∈ [ 0 ,1].
β=The probability that a potential failure will develop to a functional failure that is recorded as a corrective maintenance work order within a specific time limit,β∈ [ 0 ,1].
γ=The probability that a functional failure gives train delays,γ∈ [ 0 ,1].
m1=Total number of inspections [no.].
=Average train delay(minutes)(DT=downtime).
Probability of detection of malfunction is given by:

mR=Total number of potential failures(inspection remarks).
Note that the probability of detecting is a term that is used within non-destructive testing(NDT),e.g.the minimum flaw size reliably detected by a specific NDT technique.Within the frame for inspections,visual inspection is the most common type of NDT.In Equation 2,probability of detection refers to the fraction of items that does not meet their functional requirements.Therefore,the share of items meets their functional requirements.In NDT,stands for the share of items with potential failures that passed an inspection without notice.
Regarding,the probability that a potential failure will develop into a functional failure,depends on the severity of the potential failure and what time frame is under consideration.However,there is no quantitative way to calculate.It would be possible to calculate quantitatively if all potential failures would be left without action and their state would instead be monitored.In such case,it would be possible to see how many potential failures that,at a specific time,had deteriorated and turned into functional failures,and thus one would be able to calculate.However,this is not possible in practice.In practice,all potential failures will be assigned a priority depending on the severity,for example week,month or year;a high priority indicates higher.Given priorities can thus be used as an indicator to determine.
The probability that a functional failure gives train delay(γ)is decided by the fraction of functional failures giving that have given train delays.Within the Swedish railways,this number is approximately 25%(Table 1).
The average train delay()in Equation 1 is based upon the direct train delay that a certain item or a failure can cause.
does not take into account the indirect effects of degraded items.Such an indirect effect is for example poor track geometry,which can give train delays through temporary speed restrictions,but also greater dynamic stresses in the track and rolling stock.But on the other hand,maintenance limits are set to avoid accelerated degradation,e.g.for track geometry,limits are set to,among other things,to prevent unnecessary degradation on rolling material.
Maintenance data was collected from Trafikverket and constitute of infrastructure related corrective maintenance,i.e.functional failure data,maintenance inspections and rectification of potential failures.The collected data include seven railway lines that together consist of 65railway sections,which approximately are one third of the Swedish railway network;see Table 1 and Figure 2.
Table 1 Maintenance data


Figure 2 Assigned priorities of rectified potential failures/remarks(a),inspection types of inspections(b)and train-delaying failures per system(c)
3 Result and Discussion
The results are obtained by applying Equation 1 on the collected data;see Table 2 and Figure 3for results.The probability of detection of potential failure(α)is based only on the number of rectified potential failures(mR)with the priority week or month,which means rectification within two weeks and three months,respectively.
Table 2 Collected data

*

Figure 3 Benefit(B)in form of prevented train delays per preventive maintenance inspection
The probability of detection of potential failure(α)is based on the number of rectified weekly and monthly potential failures(mR).
From Table 2,one can see that the benefit varies significantly.A contributing factor can be that the inspection comprises off both safety and maintenance inspections,which depend on the system or component under inspection.Moreover,certain inspections of very rare but critical functional failures can be made in large numbers as they are absolutely not allowed to occur,which can result in a low.Another contributing factor is the definition of inspection;for example an inspection(spreadsheet row in the preventive maintenance data base)can in theory be equivalent to inspection of a point in a system or inspection of a whole system.An example of this is an ocular inspection of a switch and crossing(S&C),i.e.turnout,in comparison to inspection of rails with NDT trains.An inspection of an S&C can in theory refer to an inspection point,a specific number of inspection points or an inspection of the whole S&C.In case of inspection with NDT train,only manually verified potential failures are recorded,which affect the analysis of the data,but in case NDT train inspections were recorded,the question is what an inspection is,e.g.a kilometer.Another such example is ocular inspection by walking along a track section.For these reasons,it can be difficult to do comparison between different systems(Table 2and Figure 3).However,when studying the same system,the definition of an inspection is more coherent,e.g.for comparing the benefit of preventive maintenance inspections of S&Cs among railway sections for best practice.
Since all the collected data are only for one year,the proportion of rectified week and month potential failures,registered in the end of the year,are lower than earlier in the year.This effect is counterbalanced by that rectified week and month potential failures are higher at the beginning of the year.
Of all the rectified potential failures,the rectified week and month potential failure stands for 92%(Figure 2).After the inspection personnel’s judgment,and according to the maintenance policy,the risk for functional failures starts to increase for 92% of the registered potential failures after two weeks(week remarks)or three months(month remarks);see Figure 4.However,the time when the potential failures degrade to functional failures in practice,and thus recorded as corrective maintenance,is unknown.Trafikverket’s(Swedish Transport Administration)experience is that a large proportion of the potential failures that are not rectified within the stipulated time have not lead to functional failures.This means that(β)will have to be set based on expertise about systems in the railway and their failure modes.This can be accomplished by maintenance personnel,and if possible,in conjunction with revision of the guidelines for setting of potential failures priorities.In this study,β was set to arbitrary 0.75,which from the above discussion can be seen as very high.However,it was set to 0.75 with the starting point that all the potential failures that passed its given priority time,for example,week or month,were re-registered as functional failures.This gives indeed β of 92%,since it was chosen to be calculated by using rectified week and month potential failures.But 92% were seen as high since potential failures that pass their priority time in practice were not transferred to the functional failure data base,and therefore the 92% were rounded down to the nearest quartile i.e.0.75.Also,note that by assessment of expertise,β will be given different values for different systems and failure methods,and possibly a value close to zero in many cases.Nevertheless,degradation to functional failure is certain when time goes towards infinity.
Table 2 and Figure 3 show the benefit of from inspections of various systems,however,35.1%(2154/6131)of all train delaying functional failures are of the type fault disappeared(Figure 2),and are therefore hard to link to the inspections.These 35.1% are included in the average train delays()in row“65 railway sections” in Table 2,but not in the other rows since they are per system or component.The problem with the errors disappearing in general can be solved in Söderholm(2007).

Figure 4 Illustration of reasoning at potential failures
4 Conclusions
A formula has been described for calculating the relationship between preventive maintenance inspections and train delays for rail infrastructure.When an inspection is performed,the probability to find a potential failure is between 0 and 100%.The potential failure is registered as an inspection remark.The risk that the potential failure will degrade to a functional failure within a certain time is also between 0and 100%.As an example,one can assume 100inspections,with 10% probability to find a potential failure,75% risk for functional failure if an action is not taken within a near future and 25% risk for train delays.This gives 100×0.1×0.75×0.25=1.875 prevented train-delaying functional failures,and therefore 1.875 times the average number of train delay minutes in reduced minutes of train delays
A case study was carried out to verify the method.The results show that the prevented train delay minutes per inspection for different systems within 65 rail sections is between 0-40minutes per inspection(Table 2 and Figure 3).This relationship depends,however,to a large degree on the definition of inspection.One should therefore investigate what the recorded inspections pertains to,for example,a recorded inspection in the preventive maintenance database can in theory pertain to an inspection point in a system or an inspection of a whole system.The relationship also depends on the type of inspection,i.e.safety or maintenance inspections.Finally,the relationship depends as well on the criteria used for the assigning priority to potential failures.
Acknowledgement
The authors wish to appreciate the financial support provided by National Natural Science Foundation of China(No.51208034,No.U1234211)and Fundamental Research Funds for the Central Universities(No.2015JBZ012).
References
[1]CEN,2010.EN 13306:Maintenance Terminology[S].European Committee for Standardization(CEN).
[2]Nissen,A.,2009.LCC for Switches and Crossings at the Swedish Railway:A Case Study[J].International Journal of Condition Monitoring and Diagnostic Engineering Management Comadem,12(2),10-19.
[3]Parida A.,Stenström C.,Kumar U.,2014,Performance Measurement for Managing Railway Infrastructure[J].International Journal of Railway Technology,2(4),1-14.
[4]Söderholm P.,2007.A System View of the No Fault Found(NFF)Phenomenon[J].Reliability Engineering and System Safety,92(1),1-14.
[5]Stenström C.,2014.Operation and Maintenance Performance of Rail Infrastructure:Model and Methods[D].Luleå University of Technology.
[6]Stenström C.,Norrbin P.,Parida A.,Kumar U.,2016.Preventive and Corrective Maintenance:Cost Comparison and Cost-benefit Analysis[J].Structure &Infrastructure Engineering,12(5):603-617.
ICRE2016-International Conference on Railway Engineering