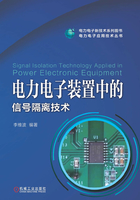
1.3 应用于PEE中的典型隔离技术
1.3.1 隔离驱动技术
1. 应用概述
可控型功率器件驱动电路中,驱动信号的产生一般会采用微控制器(MCU),MCU可选的类型较多,如单片机、DSP和ARM等。MCU产生驱动信号的方式,主要采用闭环的形式,对比给定信号和反馈信号,结合系统所采用的控制策略,以PWM信号形式进行输出,每个可控型功率器件对应一路PWM信号。为提高可控型功率器件电路的可靠性,驱动信号隔离技术经常被采用。图1-9a所示为带隔离变压器并网逆变器的拓扑图。需要实时采集电流iLabc、ipabc;实时采集电压upabc,还需要借助必要的隔离手段(如电流和电压传感器、隔离放大器和隔离A/D转换器等),方能满足在具有强电磁干扰环境中安全获取弱信号的工作需求。
图1-9b所示为隔离型驱动电路原理框图。考虑到PWM斩波控制的对象为高压信号,且电路中的电磁干扰较为严重,因此隔离芯片经常被采用,以提高电路的可靠性。隔离芯片主要用于实现高压侧和低压侧的电气隔离。另外,隔离芯片输入侧和输出侧的信号,在电源及地线方面不能共用,经常通过DC/DC隔离电源模块,实现电源和地线的电气不互连。对于可控型功率器件来说,其驱动信号存在诸多要求,如电压幅值、上升时间和下降时间等。在实际电路的设计过程中,通常采用专用的驱动芯片,实现驱动信号的放大,以满足驱动信号的不同需求。IR系列芯片,如IR2103、IR2104、IR2110、IR2130和IR21844等,广泛应用于可控型功率器件的驱动信号的功率放大环节。可控型功率器件在DC/DC、DC/AC、AC/DC和AC/AC 4种电力电子变换器中,存在广泛的应用。依据被可控的程度,可分为半控型功率器件和全控型功率器件。前者的典型代表芯片为晶闸管;后者的典型代表芯片为MOSFET和IGBT。基于硅的功率器件,几乎占据了整个电力电子装置市场。随着槽栅、FS和SJ等半导体生产技术的提升,基于硅的可控型功率器件的制造技术遇到瓶颈。宽禁带半导体器件在耐压、过电流、开关速度、散热等方面的优势,使得该类器件具有较大的发展空间。目前,已有成熟的碳化硅MOSFET产品面世。

图1-9 并网逆变器及其隔离驱动示意图
2. 基于光耦的隔离驱动技术
当前,应用于可控型电力电子装置的隔离驱动技术主要分为3大类:
1)光耦隔离;
2)磁变压器隔离;
3)光纤隔离。
光耦隔离驱动的典型代表就是输出高达2A且带过电流保护的IGBT驱动光耦HCPL-316J。该光耦可驱动最高为150A/1200V级的IGBT,具有光学隔离、带故障反馈输出、CMOS/TTL兼容、500ns开关速度、软关断技术、集成过电流、欠电压保护、15~30V宽压工作环境以及-40~150℃工作温度等显著特点,图1-10所示为它的典型应用电路示意图。

图1-10 基于光耦HCPL-316J驱动IGBT三相逆变桥的典型电路示意图
如前所述,光耦隔离技术具有如下优缺点:
(1)光耦隔离驱动技术具有如下优点:
1)成本低;
2)芯片设计制造简单;
3)输入信号的频率可以高达数十MHz。
(2)光耦隔离驱动技术具有如下缺点:
1)传输延迟较大;
2)开关速度较慢,对信号的前沿和后沿产生较大的延时;
3)多路应用中,各个光耦器件的参数需要一致,增加了电路设计的难度。
3. 基于磁变压器的隔离驱动技术
磁变压器隔离驱动技术的典型代表就是ADUM系列芯片,它们是ADI公司生产的ADUM系列芯片(称作iCoupler数字隔离器),该系列芯片将CMOS技术和芯片尺寸变压器有机地结合起来,其基本原理如图1-11所示,图中所示的变压器进行能量和信号传输时,无电气特性直接相连的情况。实现磁变压器隔离的典型器件具有高数据速率,能够适应于DC~100Mbit/s的数字信号,兼容3.3V和5.0V工作电压/电平转换,可作为光耦的替代产品使用。
从图1-11a和b可以看出,磁变压器隔离器的输入信号经过一个施密特触发器进行脉冲信号调整,使输入的波形为标准的矩形波。磁耦还独具直流校正功能,图中的两组线圈起到脉冲变压器的作用,输入端逻辑电平的变化会引起一个窄脉冲(2ns),经过脉冲变压器耦合到解码器,然后再经过一个施密特触发器的波形变换输出标准的矩形波。如果输入端逻辑电平超过2μs都没有任何变化,则校正电路会产生一个适当极性的校正脉冲,以确保变压器直流端输出信号的正确性;如果解码器一端超过5μs都没有收到任何校正脉冲,则会认为输入端已经掉电或不工作,由看门狗电定时器电路,将输出端强行置为高电平。并且磁变压器隔离产品的功耗仅为传统光耦的1/10~1/60,速度最高可达150MHz,最多可集成4个通道,且通道方向分布灵活,大大缩短了研发周期。磁耦数字隔离器的最高隔离电压是5kV,最高绝缘电压是600V,最低瞬态共模抑制能力(CMTI)是25 kV/μs。

图1-11 典型磁变压器隔离芯片原理框图
采用磁变压器隔离驱动技术具有以下优点:
1)输入信号的频率可以高达百MHz级;
2)单个芯片可以实现多路信号的隔离,在多个可控型功率器件的联合控制过程中,具有独特的优势;
3)属于电压型器件,外围电路设计较简单。
磁变压器隔离驱动技术具有如下缺点:
1)芯片价格较高,目前主要采用国外的ADUM系列器件(如单通道AD-UM1100,见图1-11b)实现;
2)强电磁环境下应用的可靠性较低。
4. 基于光纤的隔离驱动技术
使用光纤隔离驱动技术时,安捷伦(Agilent)的HFBR系列器件就是典型代表。通过光纤进行驱动信号隔离时,一般由发射器和接收器两个部分构成。发射器和接收器由两个独立的部件构成,有别于光耦件的接收和发射在同一部件上。光纤隔离驱动技术的基本工作原理如图1-12所示。

图1-12 光纤隔离驱动技术的原理框图
图1-12所示的这种隔离技术在实现过程中,接收器借助内部集成的LED灯,发出nm量级波长的光波。借助于光纤,光波将会被传送到接收端。接收器在接收端将光波解码后,控制可控型功率器件执行开通和关断操作,进而输出高低电平。
当前,绝大多数光纤隔离,都采用安捷伦公司的HFBR-0400产品系列,发射器有HFBR-1402、-1412、-1404、-1414型; 接 收 器有HFBR-2402、-2412、-2406、-2416型。如图1-13所示为HFBR-1414TZ和HFBR-2412TZ的实物图。

图1-13 光纤头HFBR-0400产品系列实物图
光纤隔离驱动技术具有以下优点:
1)输入信号的频率可以高达MHz级;
2)传输距离远;
3)抗电磁干扰性能好;
4)隔离电压等级高。
光纤隔离驱动技术具有以下缺点:
1)同时实现多个驱动信号的隔离,所需的外围部件较多;
2)光纤的机械强度较低,使得光纤易损坏;
3)光纤接口处理需要特殊的设备,制作较困难。
1.3.2 多路数据采集系统的隔离技术
1. 应用概述
电力电子装置中的数据采集系统(Data Acquisition System,DAS)是指A/D转换器在时钟控制下,将来自传感器(如电压、电流和温度等传感器)和其他待测设备产生的连续模拟信号(如电压、电流和温度等)转换成离散型的数字量信号,整个采集过程中结合计算机进行自动采集。由于计算机无法识别上述传感器输出的模拟信号,因此采集系统将模拟信号转换为数字信号,这样数字信号就可以与计算机进行数字通信,将采集到的数字信号送入计算机,从而实现在计算机上获得采集的信息。
常用的PEE设备在进行多个检测点同时采集数据时,由于多路采集信号的电势参考点不同,而输入信号之间会因存在电势差而引起相互干扰;采集过程中模拟部分与数字部分之间的参考点不同,也容易引起模拟信号和数字信号之间的相互干扰。为此,常规的做法就是:通过多通道信号隔离以及供电电源隔离等不同措施,实现各路激励电源和采集信号分别进行转换,就可以有效地抑制干扰成分,也就能够设计出满足实际要求、电路简单和采集精度高的带隔离型多路数据采集系统。有关这个方面的研发工作一直备受PEE设备的关注。
因此,为了保证信号间的有效传输,减少信号在传输过程中出现失真或干扰等不利影响,通常选用信号隔离技术。信号隔离就是需要将输入单路(多路)电压(或电流)信号,利用信号隔离器件变送输出原来输入前的信号,切断了信号输入、输出以及电源之间的电气干扰。信号隔离器是一种输入、输出设备,它接收输入信号,转化成一种与输入成一定线性关系的输出信号,然后传送给上位机或者其他通信设备。信号隔离器通常是利用光电隔离或电磁隔离方式,切断输入信号与输出信号之间的电气连接途径,从而实现信号间的电气隔离,同时也不会影响信号的可靠传输。且在实际工程实践中,常常还要在隔离技术中增加信号的运算、分配和滤波等调理功能。
2. 信号隔离技术
图1-14a所示为电机调速系统的典型拓扑,需要获取:
1)直流母线的电压VDC、电流IDC;
2)输出交流电压VU、VV、VW,电流IV、IW;
3)位置(速度);
4)冷板温度。
图1-14b所示为应用于电机调速系统中的多路信号调理电路的原理框图,它采用多个A/D转换器同步并行采集,即一路信号采用一个A/D转换器进行采集,然后将采集的数字量通过数字量隔离芯片传送给CPU模块(或多CPU协调系统)。该方案可以实现多个A/D转换器同步并行且隔离采集,但需要多个A/D转换器和多个独立电源供电才可以达到隔离的效果,成本较高且尺寸较大。
图1-14b所示的信号调理电路,它是将信号感知部分产生的电信号或电流信号进行信号调理放大以及由电阻电容组合滤波处理。信号调理放大电路,可以选择精密运放组成,如可以选择单电源(3~30V)、轨到轨、低功耗、FET输入的运算放大器AD824进行信号调理处理。通过调理电路处理,信号可以达到A/D转换器采集电压的工作范围。作为信号转换部分的A/D转换器,是整个工作过程快慢的决定性环节,是由后续核心控制(CPU模块)部分发送相应的控制时钟进行的,所以A/D转换器的采样速率和精度与后端核心控制单元密切相关。
当然,如果考虑到数据采集系统的体积和成本因素,可以采用多通道切换的设计思路。多路信号在隔离采集时,各个通道的选择可以采用电子开关(模拟开关)对它们依序进行切换。信号从模拟开关出来后,经过隔离芯片进行模拟量隔离,再传递给A/D转换器进行离散化处理,整个测试系统的原理框图如图1-15所示。

图1-14 应用于电机调速系统中的数据采集系统的原理示意图
信号调理部分包括信号的调理、多通道切换以及模拟信号隔离等。可以采用一个公共的差分A/D转换器,信号采集时使单路信号的正负端同时切换,在A/D转换器的前端可以采用多通道切换芯片进行通道选择。现将关键性器件的选择简述如下:

图1-15 多通道切换的数据采集系统的原理框图
1)隔离器件可以选择2.5kV(有效值)级的隔离放大器ADUM3190或者5kV(有效值)级的隔离放大器ADUM4190,它们具有宽电源电压范围(3~20V(VDD1和VDD2))、3dB输出的带宽典型值为400kHz等显著优势。
2)多通道切换芯片,可以选择ADG1206,它是低电容、16通道和±15V/12V的iCMOSTM多路复用芯片,具有电源电压范围宽(33V)、导通电阻小(≤120Ω)、轨到轨工作模式和兼容3V逻辑兼容输入等显著特点。
3)A/D转换器芯片,可以选择单通道通用输入模数转换前端AD4110-1,它内置24位A/D转换器的通用输入模拟前端,适用于工业过程控制系统。它针对电流或电压信号可以通过软件配置高压输入,并且允许直接连接所有标准工业模拟信号源,如±20mA、±4~20mA、±10V和所有热电偶类型。针对回路供电的电流输出传感器可提供现场电源。AD4110-1提供内部前端诊断功能,用于指示过电压、欠电压、开路、过电流和过温情况。高压输入具有热保护、过电流限制和过电压保护功能。AD4110-1集成了精密24位∑-Δ的A/D转换器,转换速率为5SPS~125kSPS(Sample Per Second,每秒采样次数),并且具有50Hz和60Hz噪声同时抑制的特性。
图1-16所示为多通道切换的数据采集系统组成框图,现将它的构建方法简述如下。
模拟部分电路主要负责多路信号的调理、选择和隔离,包括信号调理电路、模拟开关和隔离运放。数字部分电路主要包括A/D转换器、CPU模块和数字信号处理等,用于完成模拟信号的离散化、数据运算处理和协调系统动作等工作。供电部分包括两个隔离型DC/DC和EMI滤波模块,DC/DC1模块为隔离前端电路系统的供电电源,DC/DC2模块为隔离后端电路系统工作的供电电源。多路模拟信号经过输入保护及信号调理模块后进入多路选择器,经过一个模拟信号隔离运放后传送到高速A/D转换器完成单路模拟信号的数字量化。CPU模块经由高速A/D转换器的控制信号作用才能进行数据流的交互。虽然图1-16位并没有示意出来,为了读者方便理解,需要将高速A/D转换器的基本处理思路简单说明一下,即在高速A/D转换器量化后的数据进行数字滤波处理后,将该数据流回传给它的FIFO缓冲器输出,并经过串并转换编码模块后,才能进入CPU模块。在控制信号作用下,将储存于CPU模块中的数据通过接口电路从CPU模块中移出至输出端,经过通信接口电路输出至上位机。需要提醒的是,如果所选择的CPU内置有A/D转换器,且它的运算速度和精度都可以满足要求时,就可以省掉外置的A/D转换器。

图1-16 多通道切换的数据采集系统组成框图