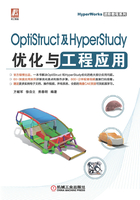
3.4 工程实例
3.4.1 电池包外壳形貌优化
随着电动汽车的普及,动力电池的性能越发受到重视。电池包壳体的固有频率对电池包总体的NVH(噪声、振动、声振粗糙度)性能影响较大,若要提高壳的固有频率,可加厚壳体或者在壳体上生成合适的拉延筋。本节展示了形貌优化中不同的对称约束方法对优化结果的影响。
本例将简要介绍电池包外壳(见图3-43)形貌优化的定义方法,并包含不同对称约束的使用方法。
优化三要素
优化目标:最大化一阶频率。
设计约束:优化区域质量上限4.5kg。
设计变量:壳体上平面。

操作视频
操作步骤
Step 01 定义形貌优化设计变量。模型中的设计区域是名为design的component。单击Optimization>topograph>create定义其为形貌优化设计变量,最小筋宽为10mm,拔模角度为60°,拔模高度为15mm,起筋方向为单元法向的反方向,详细设置如图3-44所示。

图3-43 初始模型

图3-44 形貌优化设计变量
拓展:对称约束的使用。
OptiStruct中支持不同类型的对称约束,比如常用的单平面对称、双平面对称、中心对称、线性排布和平面约束等。本节将介绍Two Planes(双面对称)、Linear(线性排布)和Planar(平面约束)三种对称方式的建模设置以及相应的结果对比。
Two Planes多用于结构存在两个对称方向的情况,在OptiStruct中,即使原始结构没有两个完美的对称面,也可以施加双面对称约束。定义双面对称约束时,只需要定义两个对称面即可,定义方法如图3-45所示,指定an-chor node、first node和second node三个点,anchor node和first node形成第一个对称面的法线方向,再加上anchor node做基准点,即可定义第一个对称面。同理,anchor node和second node定义第二个对称平面。双面对称约束定义如图3-46所示。

图3-45 双面对称示意图

图3-46 定义双面对称约束
Linear约束用于生成线性均匀分布的拉延筋,是很常见的起筋形式。其定义方法如图3-47和图3-48所示,只需用anchor node和first node定义其排布方向即可。

图3-47 线性对称示意图
Planar约束使优化结果的每个拉延筋都在一个平面内,如图3-49所示。

图3-48 定义线性对称约束

图3-49 平面对称示意图
Step 02 定义质量及频率响应。质量响应类型为mass,只考虑设计区域的质量变化,通过by entity选择设计区域对应的属性,如图3-50所示。

图3-50 质量响应
频率响应类型为frequency,考虑一阶模态,Mode Number处输入1,如图3-51所示。

图3-51 频率响应
Step 03 定义设计约束。使用Tool面板中的mass calc测出设计区域质量为4.431e-03。将mass响应定义为设计约束,其上限为4.500e-03,如图3-52所示。

图3-52 定义约束条件
Step 04 定义优化目标。电池包壳体形貌优化的主要目标是提高一阶固有频率,将优化目标设置为freq响应最大化,如图3-53所示。loadstep选择唯一的载荷步。

图3-53 定义优化目标
Step 05 提交计算。除对称约束不同外,其他参数设置完全一样,提交计算后得到下面三个结果。Two Planes约束下,拉延筋沿两个方向对称,优化后一阶固有频率为34Hz,如图3-54所示。Linear约束下,拉延筋呈线性排列,优化后一阶固有频率为47Hz,如图3-55所示。Planar约束下,拉延筋排列与Linear类似,但优化后一阶固有频率为36Hz,如图3-56所示。从固有频率来看,Linear约束得到的结果是最优的,因此在优化过程中,建议多尝试不同的制造约束,有更大概率得到最优解。

图3-54 Two Planes约束优化结果

图3-55 Linear约束优化结果

图3-56 Planar约束优化结果
3.4.2 拓扑和形貌联合优化
形貌优化可以为钣金件起筋,提高结构的刚度。拓扑优化可以找到主要的传力路径,去掉不重要位置的材料,从而达到减重的效果。在实际工程应用中,可能既需要通过起筋来提高结构的刚度,又有减重的需求,因此可以将拓扑优化和形貌优化联合使用,即拓扑和形貌联合优化。
在建模方法上,拓扑和形貌联合优化与纯拓扑优化或者纯形貌优化的唯一区别在于同时存在两个设计变量,即既有拓扑优化设计变量,又有形貌优化设计变量。优化响应、设计约束和优化目标定义方法与纯拓扑优化或纯形貌优化并无差异。
本例展示了在一个相机框架模型(见图3-57)上进行拓扑和形貌联合优化的过程。固定约束中间大孔上所有的节点,在边缘位置上6个孔分别加载沿X或Y轴负方向大小为1N的集中力,分为6个工况加载。另外,再加一个自由模态分析工况,共7个工况。

图3-57 初始模型
优化的目标是保证最大变形量不超过原模型、固有模态频率不低于原模型,即刚度不变的情况下,使用的材料最少,从而达到降低成本的目的。
相机框架的拓扑和形貌联合优化建模步骤可分为以下6步。
1)准备好可正常计算的分析模型。
2)定义拓扑优化设计变量,可设置最大、最小尺寸约束和对称等制造约束。
3)定义形貌优化设计变量,可设置起筋参数以及制造约束。
4)定义响应。
5)定义约束条件。
6)定义优化目标。
优化三要素
优化目标:结构质量最小化。
设计约束:6个加载点的变形量不超过原模型,前6阶模态频率不低于原模型。
设计变量:大圆孔周围的长方形区域。

操作视频
操作步骤
Step 01 定义拓扑优化设计变量。本例使用的模型为bracket_start.fem。拓扑优化可以找到主要传力路径,并保留主要传力路径上的材料,去除其他区域的材料。模型中的设计区域是名为DOMAIN的component,即大圆孔周围的区域。由Analysis>optimization>topology面板将其定义为设计空间。为避免优化后出现很小的特征,在设计变量中添加最小尺寸约束2mm。另外,相机框架总体是左右对称的,因此为模型添加对称约束,保证优化后的结构对称性。详细设置如图3-58和图3-59所示。

图3-58 拓扑优化设计变量
Step 02 定义形貌优化设计变量。形貌优化的设计区域的是名为DOMAIN的component,由Analysis>optimization>topography面板将其定义为设计空间。最小筋宽为2mm,拔模角为45°,拔模高度为0.3mm;另外,施加对称约束以保证产生对称的筋结构。详细设置如图3-60所示。

图3-59 模型对称面

图3-60 形貌优化设计变量
Step 03 定义响应。
本例中一共需要定义13个响应:6个位移响应、6个模态频率响应和1个质量分数响应。
① 6个位移响应为6个载荷施加点在相应工况下的位移,可通过Analysis>optimization>responses>static displacement面板进行定义,如图3-61所示。若位移方向不能确定,可选择total disp。

图3-61 位移响应
② 6个模态频率响应为模型的前6阶固有频率,可通过Analysis>optimization>responses>frequency面板进行定义。在Mode Number中设置提取模态频率的阶次,如图3-62所示。

图3-62 频率响应
③ 质量分数响应可通过Analysis>optimization>responses>massfrac面板进行定义,对应设计区域的质量分数,如图3-63所示。

图3-63 质量分数响应
Step 04 定义设计约束。
① 在减重的同时需要保证结构的刚度和固有频率不会降低,因此将上一步定义的6个位移响应定义为6个设计约束,保证模型在前6个线性静力学工况下的变形量不超过原始模型,如图3-64所示。

图3-64 位移上限约束
② 另外,在减重的同时,优化后结构的固有频率也不能降低,因此将上一步定义的6个模态频率响应定义为6个设计约束,保证其前6阶固有频率不低于原始模型。约束条件通过Analysis>optimization>dconstraints面板进行定义,如图3-65所示。

图3-65 频率下限约束
Step 05 定义优化目标。本模型的优化目标是最小化重量,可通过Analysis>optimization>objective面板进行定义,如图3-66所示。

图3-66 定义最小化质量分数目标
Step 06 提交计算。由Analysis>OptiStruct面板提交优化计算,如图3-67所示。

图3-67 提交计算
Step 07 优化结果解读及几何提取。
优化结果如图3-68及图3-69所示,可以看到远离加载点位置的材料都被去除了。同时,在保留材料的区域产生了相应的筋来提高整个结构的刚度。在保证结构刚度的情况下,重量由12.6g减少为8.8g,减重约30%。

图3-68 拓扑优化结果

图3-69 形貌优化结果
优化完成后,使用Ossmooth工具,根据.fem文件、.sh文件以及.grid文件提取优化后的几何模型,如图3-70和图3-71所示。

图3-70 提取优化结果

图3-71 拓扑+形貌优化结果
3.4.3 基于频响分析的车身地板形貌优化
良好的座椅NVH性能是汽车乘坐舒适性的基本保障,发动机振动是汽车中重要的激励来源,若能严格控制座椅对发动机激励的响应,就可有效提高乘坐的舒适性。本节以简易车身模型(见图3-74)为例,展示了基于频响分析的形貌优化。初始模型如图3-72所示。

图3-72 初始模型
在发动机顶部中心位置施加单位力激励,分析座椅安装点在0~50Hz范围内的加速度响应。本例将地板作为设计空间,要求整个模型质量不超过644kg的情况下,在地板上加筋以降低座椅安装点的加速度响应。模型文件中,材料、属性、载荷和分析步都已定义。
优化三要素
优化目标:座椅安装点z向加速度响应最小化。
设计约束:整个模型重量不超过644kg。
设计变量:地板上所有点的坐标。

操作步骤
操作步骤
Step 01 定义形貌优化设计变量。本例使用的模型为car_body_start.fem。将名为Floor的property定义为设计空间,最小起筋宽度为70mm,拔模角度为60°,最大拔模高度为60mm,最大起筋宽度为140mm,起筋方向为全局坐标系z轴方向,配合Bounds中将上限设置为1,下限设置为-1,从而可在z轴正负两个方向起筋;同时设置左右对称约束,保证左右对称起筋。详细参数如图3-73所示。
Step 02 定义响应。提取整个模型的质量响应,响应类型为mass,名称为mass。提取8个座椅安装点(见图3-74)z向的加速度响应,响应类型为frf acceleration,如图3-75所示。

图3-73 定义设计变量

图3-74 座椅安装点

图3-75 定义频响加速度响应
Step 03 定义设计约束。约束整个模型质量不超过0.644t(upper bound=0.644),响应选择上面定义的mass,约束名称为mass_cons。
Step 04 定义优化目标。本例的目标是最小化最大加速度响应,需要先定义目标参考(dobjref),参数设置如图3-76所示,然后将目标函数设置为minmax,如图3-77所示。neg reference表示响应为负值时的参考值(这里未勾选,使用默认值-1.0)。pos reference表示响应为正值时的参考值。

图3-76 定义目标参考

图3-77 定义优化目标
Step 05 查看优化结果。优化结果如图3-78所示,红色部分为主要起筋位置,呈C字形。最大加速度响应由12.5mm/s2减少为5.2mm/s2,降低了58.4%。质量由647.5kg增加为647.6kg。

图3-78 优化结果
3.4.4 SUV背门内板形貌优化
车门是汽车车身设计中十分重要而又相对独立的部件,主要用于缓冲来自外部的冲击、隔绝车外噪声等,以保证车辆的安全性、舒适性、密封性等。背门作为SUV车门系统中较大的开闭件,其刚度的大小对整车性能有较大影响。本节以某SUV背门内板模型为例,展示基于静力学分析的形貌优化。
由于背门尺寸及重量较大,因此需具备一定的下垂刚度,否则会导致背门出现下垂变形而无法正常关闭。如图3-79所示,本例在背门锁安装点施加集中力,约束背门铰链安装点的所有自由度,分析锁安装点的变形位移量。本例将除安装面和密封面外的区域作为设计空间,要求整个模型质量不超过5kg的情况下,在背板上加筋以降低锁安装点的位移响应。模型文件中,材料、属性、载荷和分析步都已定义。本例使用的模型为backdoor_start.fem。
优化三要素
优化目标:使锁安装点的位移绝对值最小。
设计约束:模型质量不超过5kg。
设计变量:除安装面、密封面外的内板区域作为优化区域。

操作视频
操作步骤
Step 01 定义设计空间。
针对车门背板原始设计,在背门锁安装点施加集中力1000N,约束背门铰链安装点的所有自由度,分析后得到其最大变形量为4.375mm,如图3-80所示。

图3-79 载荷施加点(初始模型)

图3-80 分析结果
现在希望通过结构优化方法,在质量不增加的情况下,降低最大变形量。整个车门背板为薄板结构,最合适的办法是保持薄板厚度不变,在原模型的基础上通过形貌优化方法增加拉延筋来提高整个结构的刚度。但增加拉延筋结构质量一定会增加,因此需要对原始设计进行调整,去除一些不重要的筋,然后通过形貌优化方法重新确定筋的分布形式。图3-81中,左图是原始设计,模型问题质量为5.55kg,最大变形量为4.375mm。右图中去掉了原始设计中的部分筋,将这部分壳单元单独设置为一个component,作为形貌优化的设计空间。修改后的模型质量为5.54kg,质量略微降低;最大变形量为4.376mm,变形量略增。
Step 02 定义形貌优化设计变量。将名为design的property定义为设计空间,最小起筋宽度为25mm,拔模角度为60°,最大拔模高度为8mm,最大起筋宽度为30mm;起筋方向为单元法向,配合Bounds中将上限设置为1,下限设置为-1,从而可在单元法向正负两个方向起筋;同时设置左右对称约束,保证左右对称起筋。详细参数如图3-82所示。

图3-81 定义设计空间

图3-82 形貌优化设计变量
Step 03 定义响应。提取整个模型的质量响应mass,响应类型为mass。提取锁安装点位移响应,响应类型为static displacement,如图3-83所示。

图3-83 定义位移响应
Step 04 定义设计约束。约束整个模型质量不超过5kg(upper bound=0.005),小于原始设计的5.55kg。
Step 05 定义优化目标。本例的优化目标是最小化位移响应,工况(loadstep)为loadcase 1,如图3-84所示。
Step 06 查看优化结果。
主要起筋位置如图3-85所示。最大位移响应由4.376mm降低为4.121mm,质量满足约束条件不超过5kg。

图3-84 定义优化目标

图3-85 优化结果
使用OSSmooth工具按图3-86所示设置导出优化后的模型文件,以便对优化结果进行分析验证。

图3-86 快速提取优化结果
对OSSmooth工具提取到的模型进行分析求解,可以初步验证优化结果是否符合预期。若分析求解失败且提示网格质量检查失败,可以在control card面板建立PARAM卡片来设置不检查网格质量,如图3-87所示。
将OSSmooth提取的模型提交计算,如图3-88所示,优化后的最大位移为4.12mm,小于优化前的4.375mm,变形量降低6%;模型总质量为5.54kg,相比原始设计的5.55kg略降。

图3-87 设置不检查网格质量

图3-88 分析结果