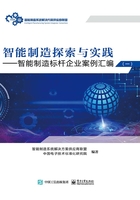
第三部分 智能制造标杆企业实践路径分析
第二部分全面展示了智能制造标杆企业概况及其变革成效。为了更好地剖析智能制造的实施经验,本章以《智能制造能力成熟度模型》(GB/T39116—2020)为基础,从智能制造能力提升的人员、技术、资源和制造四大关键方面,分析智能制造标杆企业的实践路径。
3.1 加强顶层规划设计
3.1.1 持续优化组织战略
重视智能制造战略的评测和持续优化。发展智能制造是一个流程复杂、多部门协同的系统工程,标杆企业“一把手”亲自参与其中,制定了相关组织战略和实施计划,明确了推进方向和重点任务。发展智能制造也是一个需要长期坚持的系统工程,其组织战略不是一成不变的,标杆企业通过自我总结、同行间借鉴经验等方式,定期对战略实施成效进行监控与测评,并开展持续优化,进一步提升了实施效果。
青岛海尔特种制冷电器有限公司内部设置了专职负责战略落地和实施的人员,每月形成战略评测报告,跟踪战略落地、各项指标、新建工厂进度,提出优化或改进方案。
3.1.2 激发人员创造性
建立创新管理机制,促进知识经验的数字化和软件化。创新是企业实施智能制造的关键要素,有助于催化产生先进生产方式,推动管理机制变革,加速企业智能制造进程。为更好地鼓励技术和管理创新,标杆企业探索了从传统生产要素管理到知识管理的变革之路,建立了相应的创新管理机制,有效调动了员工的主观能动性和创造性,促进了知识、技能和经验的数字化与软件化。
丹佛斯(天津)有限公司鼓励员工进行创新,每月组织员工分享展示优秀创新成果,颁发奖品,并对优秀创意进行沉淀和传播。例如,某一线员工创新了磨具的更换方法,将模具更换由2人合作完成(用时30min)降为1人独立完成(用时2min),并获得国家专利,随后该创新方法被固化成为企业标准流程。
江苏隆力奇生物科技股份有限公司针对不同类型员工的特点和需求,开发了不同的知识管理平台。针对销售人员,可以通过自主研发的“聚好平台”共享和学习销售入门知识及销售情况分析经验等。而研发人员的知识与经验收集,知识的对比、迭代,如配方的试验、升级、应用,则通过自建的“爱研系统”进行。
3.2 提高关键技术保障
3.2.1 深度挖掘数据价值
分析和挖掘数据价值,提供辅助决策支持。数据是企业转型升级过程中的重要资产,标杆企业在实施智能制造的过程中,不但能够将数据采集起来,而且能够整合各环节的数据资源,分析和挖掘数据的价值,为制造活动提供优化建议和决策支持。
新凤鸣集团股份有限公司基于采购、设计、生产、销售、物流、服务等环节的数据采集,构建了生产、销售大数据综合分析平台。该平台通过构建统一的数据集市(Data Mart)、智能辅助算法模型,构建包含70个维度、200多个KPI指标库的运营指标图,为计划调度、生产作业、销售等业务环节提供决策支持。例如,根据不同原材料的投料量、消耗量、出料量等,构建投入产出模型和月度物料平衡模型。
上汽大通汽车有限公司建立了企业级统一的数据中心,集成不同厂区、不同库的数据。基于大数据技术和现场数据,已经在多个场景取得良好效益。例如,基于神经网络循环序列模型和产品生命周期的指数模型对销量进行预测,基于网络算法、回归模型等进行生产零件物料预测等。
3.2.2 加强业务活动集成
重视设备、系统间的信息交互,实现全业务活动的集成。德国在提出“工业4.0”战略之初便将实现横向集成、纵向集成和端到端集成作为战略要点之一,可见集成工作的重要性。就内部集成而言,企业需要打通不同时期、不同厂商的IT系统和生产设施,是一个资源投入多、实施难度大的工作。标杆企业通过整体架构设计、标准规范制定及接口开发等手段,实现工厂级乃至企业级的数据贯通,提升制造过程的敏捷性,促进全业务一体化发展。
中国石油化工股份有限公司九江分公司通过自主研发,建立了生产运营企业级中央数据库(ODS),实现MES、LIMS、ERP等25个系统的集成,为调度指挥、大数据分析、三维数字化等21个系统提供数据支撑,解决了企业普遍存在的“信息孤岛”“业务孤岛”等问题。
中车青岛四方机车车辆股份有限公司通过PDM、MES、ERP、MRO、QMS等信息系统建设与集成,实现了以BOM为核心的数据贯通和以业务为核心的流程贯通,建立了全生命周期产品信息统一平台。信息平台的投入使用,减少技术工人工作量30%以上,有效提升了工作效率,节约了成本。
3.2.3 提升信息安全保障
加大信息安全投入,提升安全保障。企业将信息化设备、系统及网络等引入生产现场,有助于改善生产方式,提升智能化水平。与此同时,相关的设备、系统和网络也带来了新的安全隐患(如数据隐私泄漏等),影响现场实施效果,甚至带来无法预估的损失。标杆企业通过加大信息安全投入,借助边界防护、安全性测试等手段,建立了与之匹配的安全保障,消除了安全隐患,使防护能力得到了极大提升。
杭州西奥电梯有限公司通过工业网络安全技术(包括安全隔离、访问控制、入侵检测、加密认证等关键技术)保障信息安全,在企业管理网络中增加自学习、自优化功能,以典型的异常行为建立模型,自动上传至云平台进行分析,不断优化自身安全防护。
宁德时代新能源科技股份有限公司部署了具有深度包解析功能的安全设备及漏洞扫描设备。不仅自主研发了检测系统,对数据内容进行不间断监控,利用沙箱和行为分析找出异常时间,而且建立了智能分析系统,自动学习设备的行为并检测异常。
3.3 提升资源利用率
3.3.1 加强装备数字化改造
加强关键工序装备数字化改造,挖掘装备价值。装备作为关键生产工具,直接影响生产过程稳定性和产品质量。装备功能和性能的提升是企业实施智能制造的基本保障。标杆企业通过升级关键工序装备数据采集和分析能力,实现了运行状态的实时监测和诊断预警,提升了装备利用率和可靠性,延长了设备服役期,保障了生产过程的稳定性。此外,标杆企业借助三维模型库等新技术手段,将装备改进过程与生产工艺紧密结合,促进了产品质量的提升。
广东溢达纺织有限公司用于生产的设备中,90%具备自主研发能力。此外,该公司对关键设备进行运维和技术改造,在设计时基于三维模型库进行开发,支持对三维模型的导入、编辑、导出等管理功能。高价值关键工序设备实现了设备状态/运行数据采集、数据存储及设备状态数据展示。
长飞光纤光缆股份有限公司自主研发并完成了18种核心工艺设备的智能化提升,并投入生产应用,其提升路径分为两个步骤。第一个步骤是实现核心工艺设备的智能化。核心工艺设备与MES互通,与工厂设施系统形成过程联动,具备设备工艺环境的全参量动态计量监测功能,可基于工艺过程监测的PLC自适应工艺进行闭环控制、故障预警和自诊断修复功能。第二个步骤是基于具有时间轴的大数据系统,实现工艺过程的在线感知和实时监控。将核心工艺设备与工艺知识及智能工艺系统结合,进而实现核心工艺设备从基于工艺配方控制,提升为工艺过程自适应智能制造系统。
3.3.2 加大网络建设力度
加大网络建设力度,实现资源优化配置。网络是智能制造的基础性支撑,随着智能制造的实施,企业生产现场数据量和算力需求等激增,对网络提出了低时延、高可靠性等要求。标杆企业通过加大网络建设力度,促进了企业IT/OT融合及异构网络融合,实现了生产现场数据贯通和资源优化配置。
鞍钢集团矿业有限公司通过智能管理软件,实现对网络的远程监控和配置。该企业网络为双核心结构,采用弹性分组环技术,具有50ms故障自愈能力和高带宽利用率,具备可靠性高、吞吐量大、延迟小、丢失率低的业务保证能力,保证网络数据传输的完整性。
杭州西奥电梯有限公司通过管理平台可实现网络的远程配置,并对网络运行状态、流量使用情况、交换机配置进行监控,具备带宽、节点等的扩展和升级功能。采用双运营商、双WAN口设置,可以提供可靠性高、吞吐量大、延迟小、丢失率低的业务保证能力,结合防火墙和杀毒软件等,共同保证网络数据传输的完整性。
3.4 强化生产制造能力
3.4.1 加强迭代优化设计
加强产品设计全生命周期管理和工艺机理模型迭代优化,缩短研发周期,提升产品竞争力。面对越来越多的个性化定制需求,不仅要开展基于模型的数字化设计,而且应通过产品设计、生产、物流、销售或服务等系统的集成,实现产品全生命周期、跨业务之间的协同,最终将产品全生命周期数据反馈到设计环节,实现产品设计的迭代优化。标杆企业通过模块化设计、跨业务系统集成、协同设计及设计与工艺仿真协同等方法,缩短了产品研发上市周期,提升了市场占有率。
杭州西奥电梯有限公司通过PCS系统与PLM系统集成,研发面向个性化定制的电梯智能工厂设计模块,实现根据用户需求自动生成产品设计图纸,快速转换设备程序,并根据生产单元和生产线的能力,自动调度生产任务,从而缩短产品研制周期25%,提升产能。同时,通过SPM、PLM、LVS(MES)、QMS等系统间集成,实现销售合同签订、产品设计、生产制造过程、产品出入库、安装等业务之间的协同。产品生产、运维过程中的质量问题通过QMS、BDS(北斗卫星导航系统)等反馈给产品设计环节,实现产品设计的迭代优化。
宁德时代新能源科技股份有限公司通过产品数据管理(PDM)系统与CAX软件集成,构建研发协同管理平台,在多名模块设计工程师同步在线进行产品三维设计工作的同时,由仿真工程师借助计算机辅助工程(CAE)软件对三维模型虚拟样机进行模拟验证,求解最优设计方案,避免出现生产环节不可实现等问题,实现协同设计。在此基础上,基于三维模型驱动生成的BOM及技术文件等自动同步到ERP/MES系统,支持产品生产。
3.4.2 提升生产管控能力
1.打通采购、计划调度、生产作业、设备管理、仓储配送等主要业务,建立多要素生产管控一体化模型,提升生产过程的优化决策能力
生产是制造业价值产生的重要环节。如何在成本可控的前提下提升生产效率,是每一家企业都关注的焦点。标杆企业通过建立基于知识驱动的生产管控一体化大数据分析决策机理模型,将生产过程逐步由局部优化拓展到全局优化,最终实现生产效率的提升。
上汽大通汽车有限公司将销售预测、订单、零部件库存、排产等信息,通过自主开发的智能排产OTD系统实现集成,形成主生产计划;再通过智能排程APS系统,进行生产作业计划和调度,应用非线性逼近最佳选择的计算模型,规划出优化排程方案和详细的生产作业计划,最终实现精准拉动仓储配送和智能排产,以满足企业C2B生产模式需求。
2.建立危险源及能耗分析预测模型,实现节能减排目标
在高质量、绿色发展的大前提下,传统能源型企业普遍面临节能减排和安全环保有待改善的压力,标杆企业通过数据信息采集和模型预测分析,有效提升能源利用率,实现节能减排目标。
中国石油化工股份有限公司九江分公司将“安全环保、绿色低碳”理念置于优先位置,以打造长江最美岸线的“石化名片”为目标,构建了集HSE管理、挥发物有机物(VOCs)厂区监测、施工作业备案、环保地图、119接警处、各类可燃有毒有害气体实时联网及视频监控联动、应急指挥等系统于一体的安全环保应急指挥一体化平台,对危险气体进行异常预警分析,并通过短信等途径将数据反馈给生产相关部门,实现安全环保与生产应急联动,以此提升安全环保可控力。
巨石集团有限公司通过将MES能源管理模块、能源数据决策分析报表系统和能源采集分析系统集成进行能源管理,对各种能耗数据进行统计、分析,基于能耗分析结果对空压机、制冷机等高耗能设备进行改造和更新,通过离心空压机替代螺杆空压机的技术改造,实现年节约电能350万千瓦·时,离心式电制冷机替代蒸汽式制冷机,实现年节约电能近1000万千瓦·时。
3.4.3 提升物流供应链安全把控能力
促进物流信息透明化,提升供应链安全把控能力。企业一方面希望进一步压缩产品下线到交付客户的时间,从而减少库存,加速资金流动;另一方面希望在保障生产安全库存前提下,尽量减少原材料库存,减少资金压力。因此,保障物流信息透明化,确保按时保量送达成为关键环节。标杆企业通过仓储管理系统与运输管理系统等多系统集成,实现了物流信息透明化。借助北斗导航、大数据等相关技术,实现装载能力及运输路径优化,提升供应链安全把控能力。
安徽海螺集团有限责任公司通过“互联网+物联网”的技术应用,建设包含水泥电商平台、无人值守系统、水泥全自动包装系统、产品流向监控系统4个子系统的营销物流管理系统。通过4个子系统间无缝对接,以及电商平台与财务系统在凭证和资金方面的数据传递,形成客户“一站式”生态服务链,将互联网销售、工厂智能发运和水泥运输在线监管全面融合,实现工厂订单处理、产品发运、货物流向监控等业务流程无人化和数据应用智能化,既降低了产品库存,又提升了客户服务质量。
3.4.4 实现多渠道精准营销
建立客户需求分析模型,实现需求拉动生产制造。企业为了降低库存,提升资金链安全水平,销售前置已成为发展趋势。通过对客户需求信息的挖掘、分析,建立市场需求分析模型,实现精准营销,同时,进一步与设计、采购、生产、物流等环节联动,改进方案,缩短交期。
隆力奇生物科技有限公司通过商务智能辅助决策系统,建立销售合同订单浮动盈亏分析、销售区域分析、销售数据分析、销售均价分析、流失迹象客户分析、重点战略客户排名、回流客户分析、成品库存预警等大量数据模型,可按年、月、日趋势进行分析预测,生成相应的周期销售计划。通过SAP系统与MES、OA系统、丝路物流系统集成,实现以客户实际需求,拉动设计、采购、生产、物流,实现产销平衡,快速响应客户需求。
3.4.5 提升综合服务能力
加强客户精细化管理,提供综合服务能力。随着时代的发展,多渠道销售、个性化定制都需要提升服务能力。标杆企业通过客户精细化管理,提升客户服务满意度。同时,对于复杂产品,运用远程运维的模式为客户提供产品故障预测等服务,实现产品“一手数据”的采集,便于产品的迭代优化。
丹佛斯(天津)有限努力通过选型软件、学习网站、多款手机App,定期针对不同行业的客户提供定制化技术服务,提升客户服务质量。同时,其压缩机产品自带智能运维模块,结合终端运行监控系统,实现末端数据采集和处理,形成大数据分析基础,结合客户使用习惯进行深度分析,对故障进行预判和在线诊断。
潍柴动力股份有限公司的柴油发动机多用于重卡、公交车、校车、工程机械等,特别是用于重卡、工程机械的柴油发动机,运行时间长,工况环境差。该公司通过自主研发的ECU模块,开发智能测控及标定系统,具备发动机数据采集、状态监控等功能,并应用大数据分析进一步开发成本、寿命及故障预测等功能,为用户提供优质的售后服务及智能化增值服务,实现商业模式的创新。