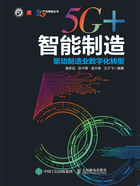
个性化定制:无缝对接用户需求
个性化定制是一种按用户需求进行产品定制和服务的生产方式。在实践过程中,制造业企业借助大数据、互联网、工业云等技术,以创建在线设计中心、用户体验中心、用户定制服务平台等互联网平台的方式对用户的个性化需求信息进行采集和对接,使用户在生产的全过程中有更强的参与感,并在个性化方面获得最佳体验,以此激发用户的消费潜力。
作为家电行业的领军企业,海尔不但致力于技术创新,而且在为用户提供个性化定制服务方面也做出了很好的示范。海尔沈阳电冰箱厂借助COSMOPlat工业互联网平台,真正做到了以用户为核心创建产品生态系统,根据用户需求为其定制产品,逐渐放弃传统的大规模制造模式,大力推行大规模定制业务,产品的不合格率大幅降低,产品的生产效率提高了79%,企业营收增长了44%,并且没有出现人们通常认为的产品定制会延长产品生产周期的问题。
作为一家生产经营高档服饰的大型企业,红领集团也在积极尝试个性化定制模式,打造了一个一体化的开放式互联网定制平台——RCMTM。收到用户的定制需求后,该平台可以在5分钟内采集人体19个部位的数据,然后根据数据库内存储的3000多亿个服装版型数据,快速为用户匹配合适的服装版型。在定制化生产模式下,红领集团的生产成本提高了10%,但设计成本减少了90%,生产周期缩短了50%,库存趋近于零,总体来看经济效益得到了大幅提升。
随着新生代消费群体的崛起,定制需求逐渐旺盛。新生代消费群体对品牌的认识更加独到、深刻,希望借助产品彰显个性,简单的功能性产品无法满足他们的需求。在新的产销关系中,企业需要深度掌握用户的个性化需求,在大规模定制方面提升能力,以赢得新生代消费者的青睐。
若要实现个性化定制模式的落地,制造业企业需要提高产品个性化、部件模块化、零件标准化的重组速度,促进生产制造关键环节柔性化改造和组织调整,创建能够动态感知消费需求的设计、制造及服务新模式。
例如,中航第一飞机研究院研制的“新飞豹”轰炸机用到了数字样机技术,切实提高了轰炸机各部件的模块化设计水平,最终形成了54000多个结构件、43万个标准件,使设计周期缩短了68%,设计返工时间减少了30%。
上海外高桥造船有限公司拥有现代化程度较高的大型船舶总装厂,针对豪华邮轮设计创建了一个大型协同设计平台,可以与国外的设计公司进行合作,共同致力于邮轮设计,并简化向船东 [1]送审图纸的流程,可以根据船东反馈对设计方案进行实时修改,切实满足船东的个性化需求,将豪华邮轮的设计效率提高了30%。
5G在智能制造领域的落地,将大大提高产线的灵活性和柔性程度,为大规模普及柔性化生产奠定基础。一方面,在工厂中应用5G网络,不但能缩减机器之间连接线缆的成本,还能凭借连续覆盖、高可靠性的网络,让机器实现自由移动,按需抵达每个地点,在各个场景中不间断工作并对不同的工作内容进行平滑切换。另一方面,5G能够建立起以人和机器为中心的连接工厂内外的全方位信息生态系统,做到信息实时共享。企业的产品设计和生产过程由客户亲自参与,产品状态信息也能被客户实时查询。